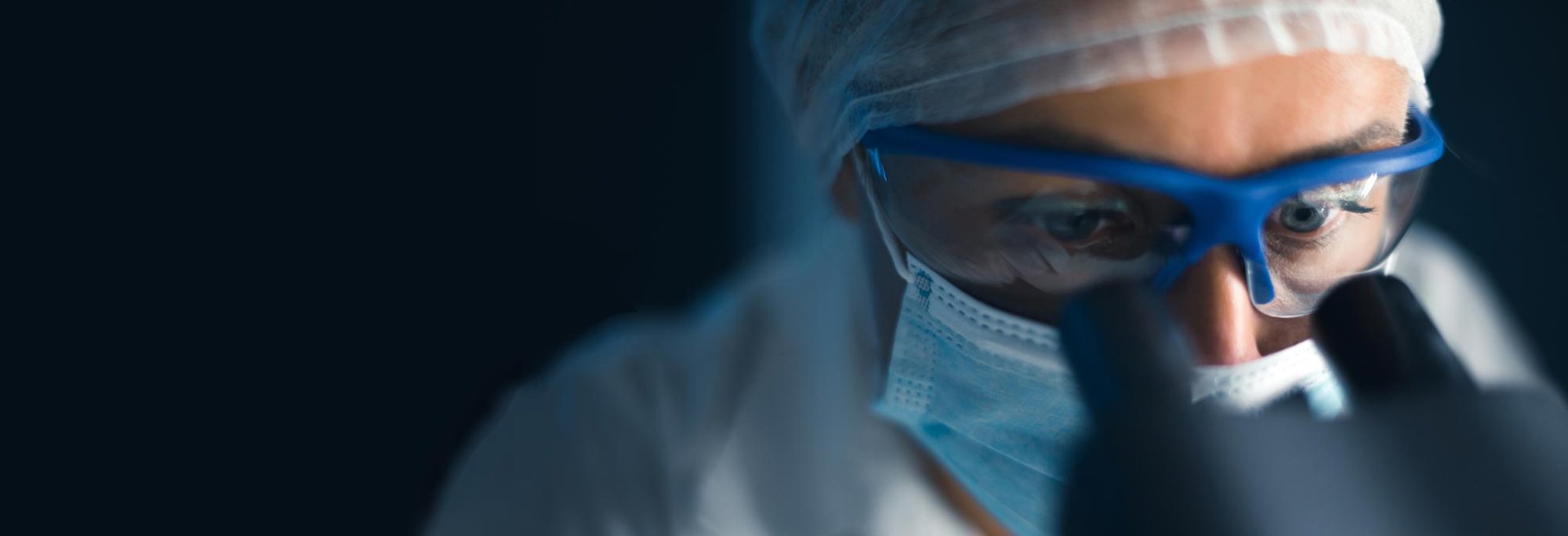
eQMS Solutions for the
Life Science Industry
A validatable solution for eQMS that puts safety and quality first
CANEA ONE is a validatable standardized system with features specifically tailored for Life Science companies.
Product quality, safety and customer satisfaction. Three factors that are extremely important for companies in the pharmaceutical, biotechnology and medical device industries. With these in mind, we have developed an easy-to-use, flexible and scalable system to help you meet the requirements of regulations and standards.
Verified standard system
We ensure that every release of CANEA ONE can be validated against the requirements of FDA Part11, GxP, GMP, MDR, ISO 13 485, Eudralex Vol 4 etc.
Use cases
CANEA ONE is currently used for most of the needs when it comes to Document Control & Quality Cases but has the capacity for more than that.
Data privacy & patient safety
Extensively tested and validated features for e-signatures, audit trail, read & distribute receipts,
competence tests etc.
Intuitive system with efficient implementation
A very user-friendly system that, through well-proven concepts of configurations and
validation can be implemented with efficiency and quality.

Challenges
in Life Science
Developing new medical innovations that are effective and safe for patients is advanced, time-consuming, and costly. It often takes many years and is a demanding process because the product, in addition to having to work, also has to be safe and suitable for large-scale production. The industry is heavily regulated, with requirements and standards to comply with and authorities that make decisions on approval of new products for the market.
Another major challenge is to create efficient and user-friendly ways of working, while meeting the requirements of both authorities and clients. Many fail to create a management system where it is easy to find, manage and maintain documents, procedures, cases and processes. This often leads to unnecessary administration, reduced transparency and overview, increased risk, and difficulties in meeting requirements.
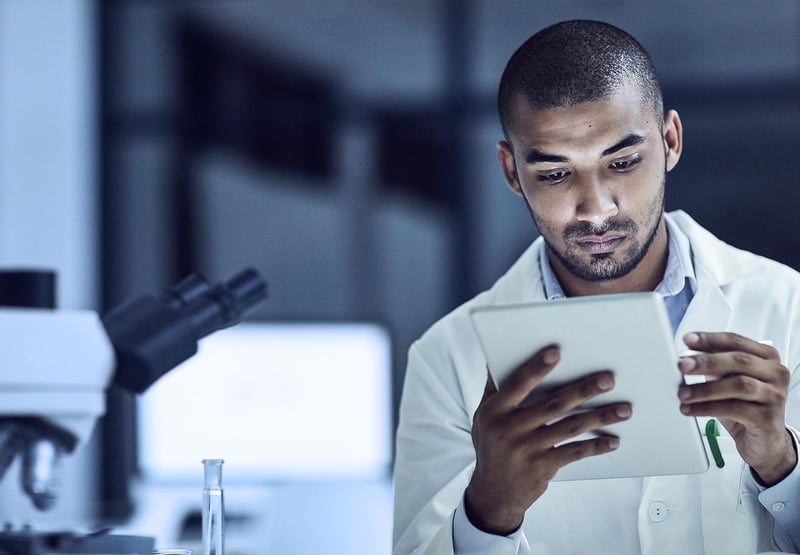
CANEA’s solution
To facilitate the work in Life Science, we have developed CANEA ONE - a validatable solution built from the ground up from a management systems perspective. Based on 20 years of experience in management systems and designed to be easy to get started with, use and maintain. CANEA ONE is a system with ready-to-use features for e-signatures, audit trail, read & distribution receipts, competence tests etc.
We work with a number of leading companies operating within the medical, biotechnology and pharmaceutical industries, but also support newly established companies in work to comply with regulatory requirements. To date, we have successfully delivered over 250 implementation projects to our clients in the EU and US.
Features
CANEA ONE is a proven and validatable complete
solution with tailored and powerful functionality.
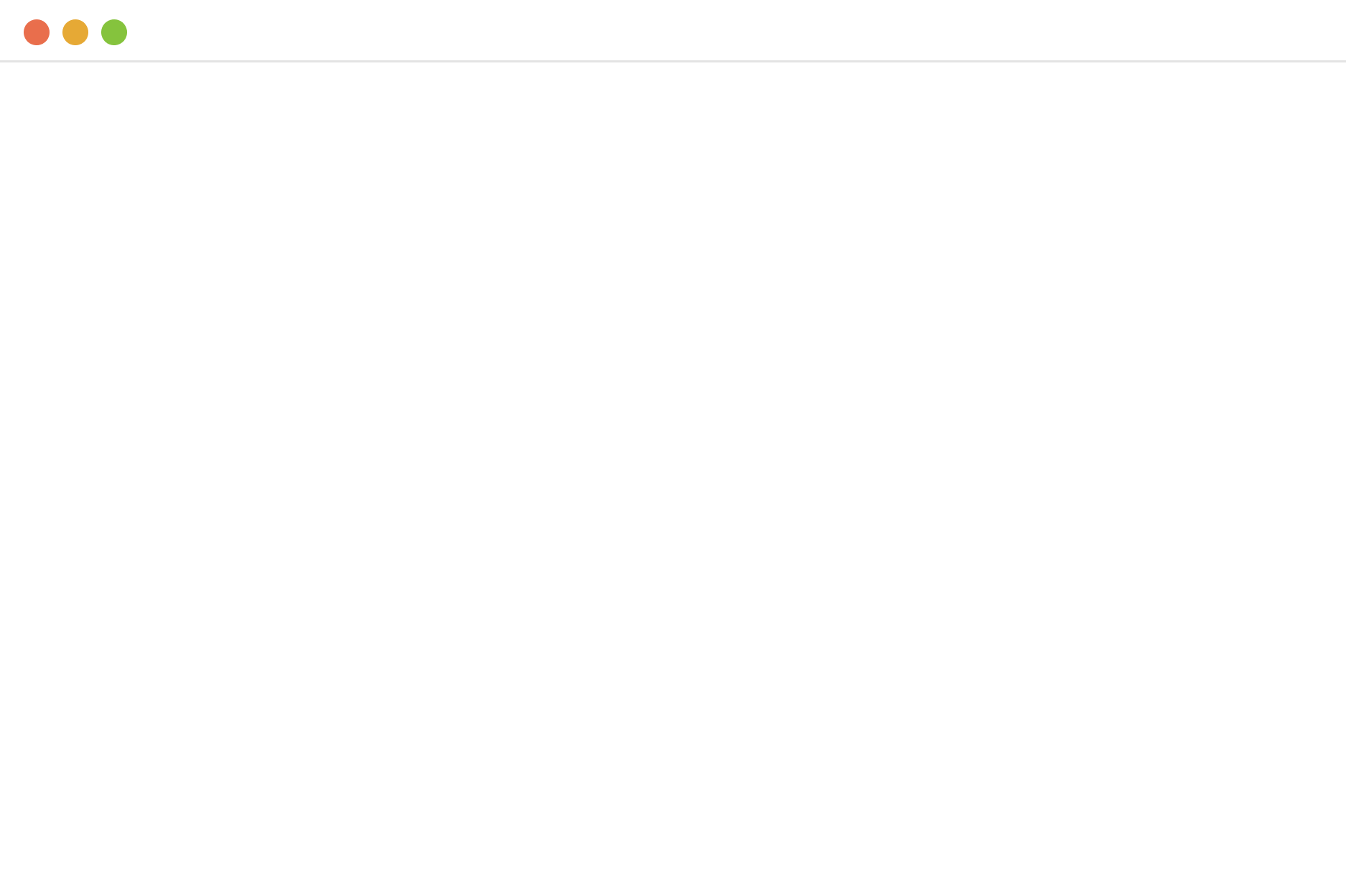
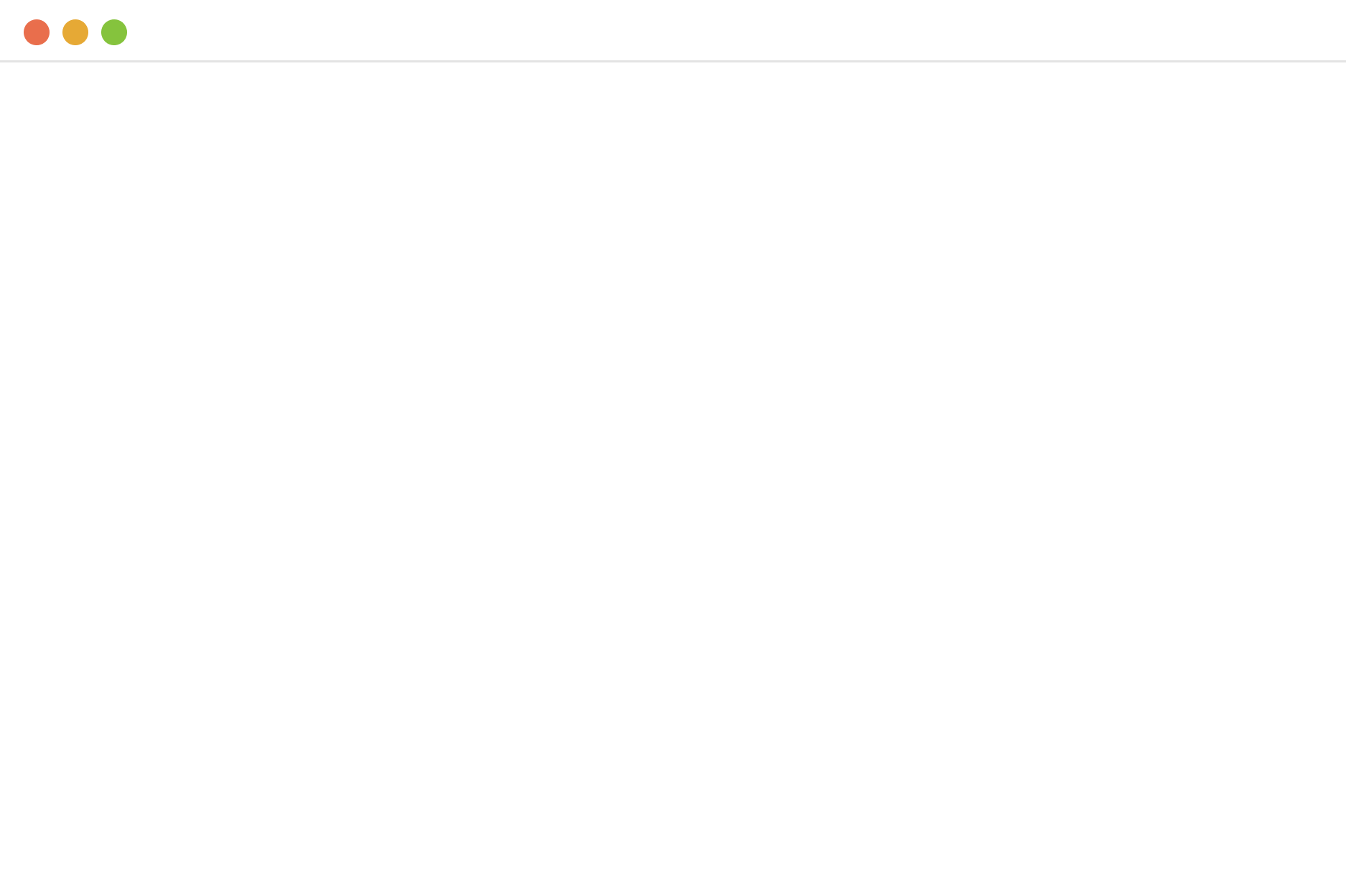
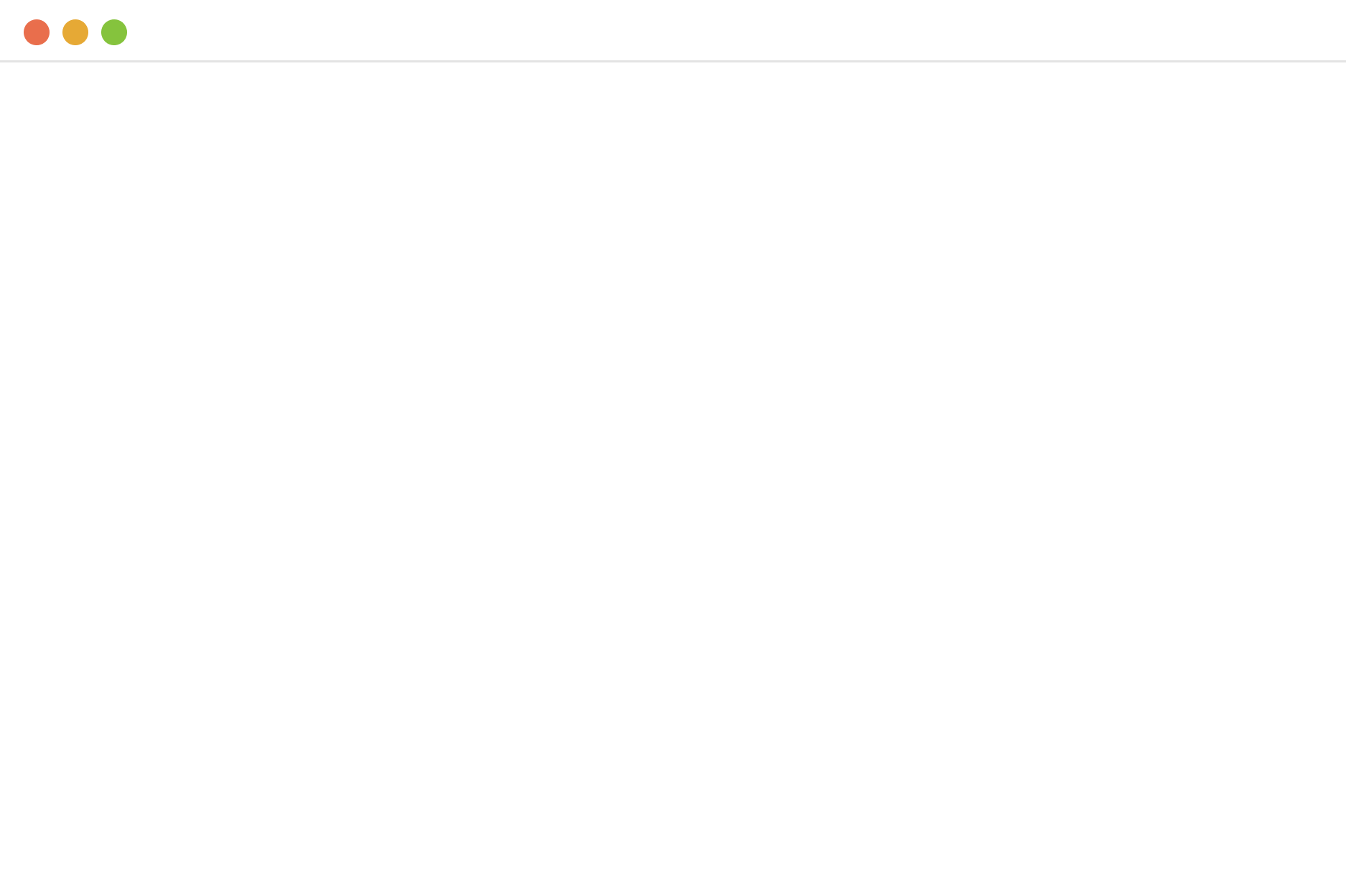
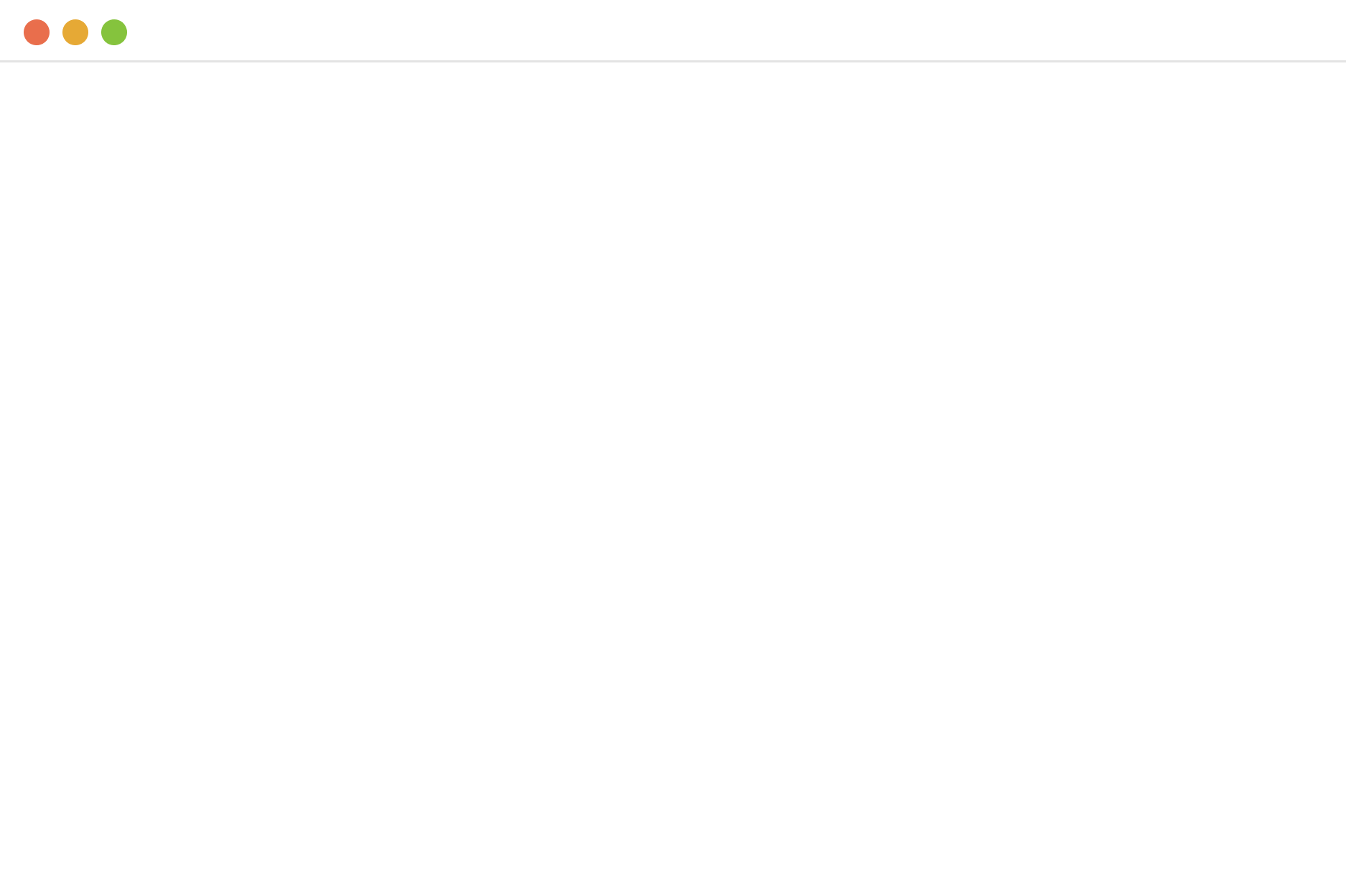
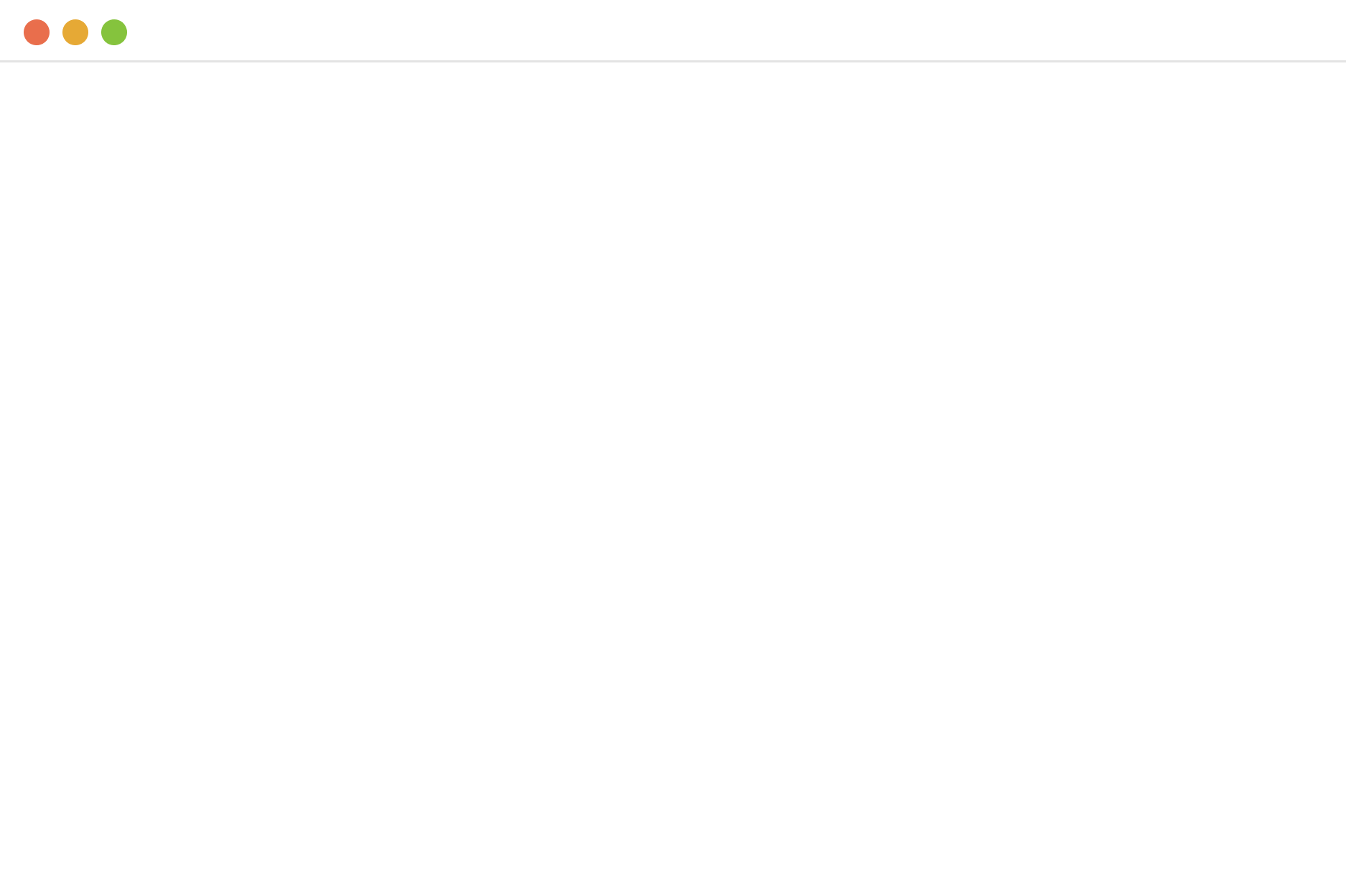
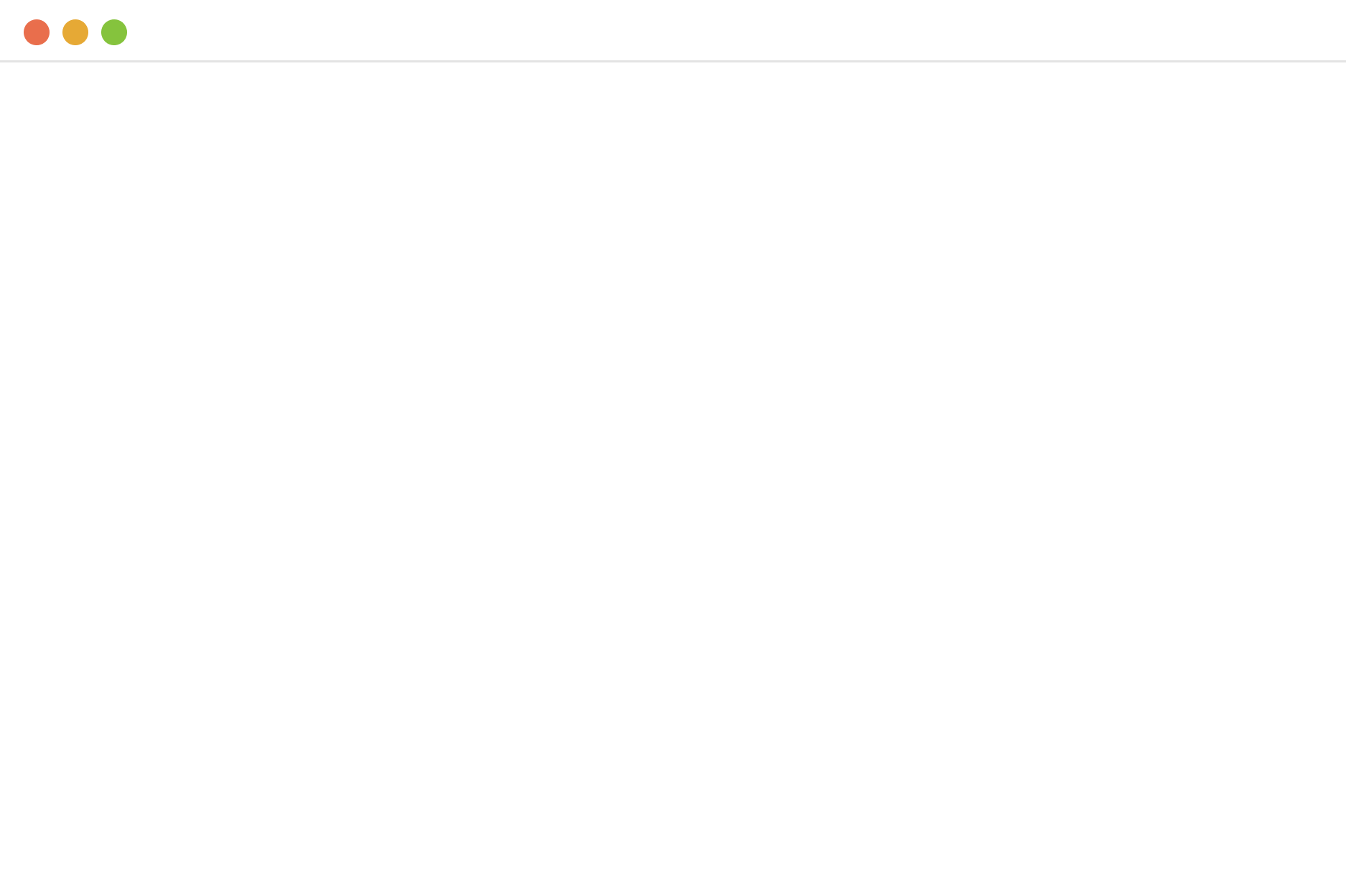
Securely manage all your instructions, procedures, checklists and other governing documents. Easy document upload and editing with support for templates, version management, review flows, permission management etc. Follow-up on the distribution of your documents is made easy through read receipts and built-in tests for competence assurance, which are acknowledged by the user with electronic signature.
Automated physical distribution of documents to bulletin boards, consultants, suppliers, clients etc. CANEA ONE is also used by many of our clients to manage their product documentation.
CANEA ONE's workflow management has been successfully used by our clients for many years to handle quality issues such as: non-conformances, changes, complaints, improvement work, corrective actions, preventive actions, audits, supplier evaluations, risks etc.
With these managed and controlled processes, efficiency & quality assurance and better process compliance are created. With follow-up and statistics features, deviations such as product defects can be systematically analyzed and eliminated. Ability to determine the root causes of problems and prevent these in order to safeguard quality and safety in your processes and your products.
Create graphical analyses with any content from all the data in your cases. You can easily extract them to attach to reports or use the analyses for future meetings where, for example, at a weekly meeting you can quickly identify the number of pending complaints per process and see the person responsible, combined with data on how long the complaint has been pending etc.
It is also easy to save the prerequisites for the analyses and combine several different analyses on a separate home page that each time you click on it can, for example, give you updated analyses from several different areas, departments, sites or with different types of data.
Decision support through visualization and monitoring of gathered data in both table and diagram form. Easily generate statistics and retrieve aggregate information from the system. Create analyses with optional content and produce reports for presentation in PDF or PowerPoint, for example. Provides well-organized views from a general level right down to a detailed one.
Create conditions for successful projects, delivered on time and within budget. With support for your project models and project working methods, the project team has access to tools for, among other tasks, time management, risk management, document management, budgeting, status reports and resource planning. Option to review and prioritize projects in the project portfolio with complete status information for each ongoing project. Financial control, budget follow-up and an embedded communications flow in the project tool that gathers all internal and external communication in one place.
CANEA ONE is currently used by our clients for more than just quality management, how about being able to manage HR issues such as recruitment, onboarding/offboarding in the same system? Or why not manage your internal service issues like ordering new phones, getting help with the computer or maybe safety classifications/authorizations etc.
Other inspirational examples are the Safety Database for reporting to Eudamed or why not a supplier register where your planned and performed audits, evaluations etc. are summarized. Project ideas that can be collected, analyzed, decided and prepared with a checklist before the start of the project. The workflow management in CANEA ONE can be used for a wide range of needs.
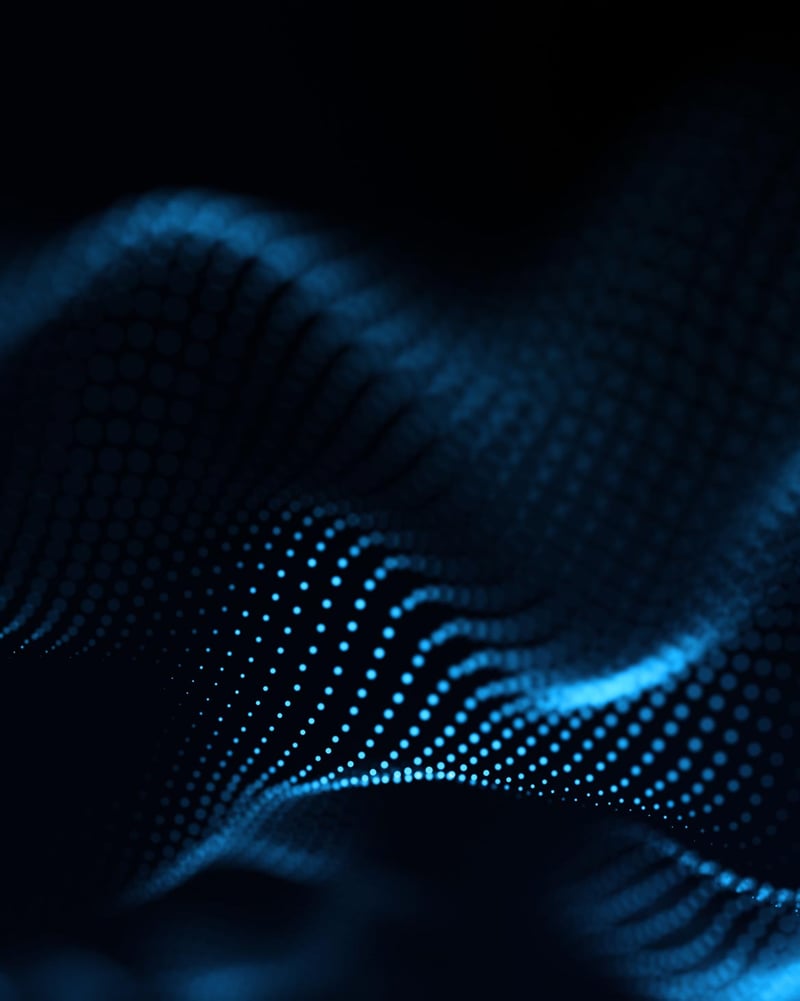
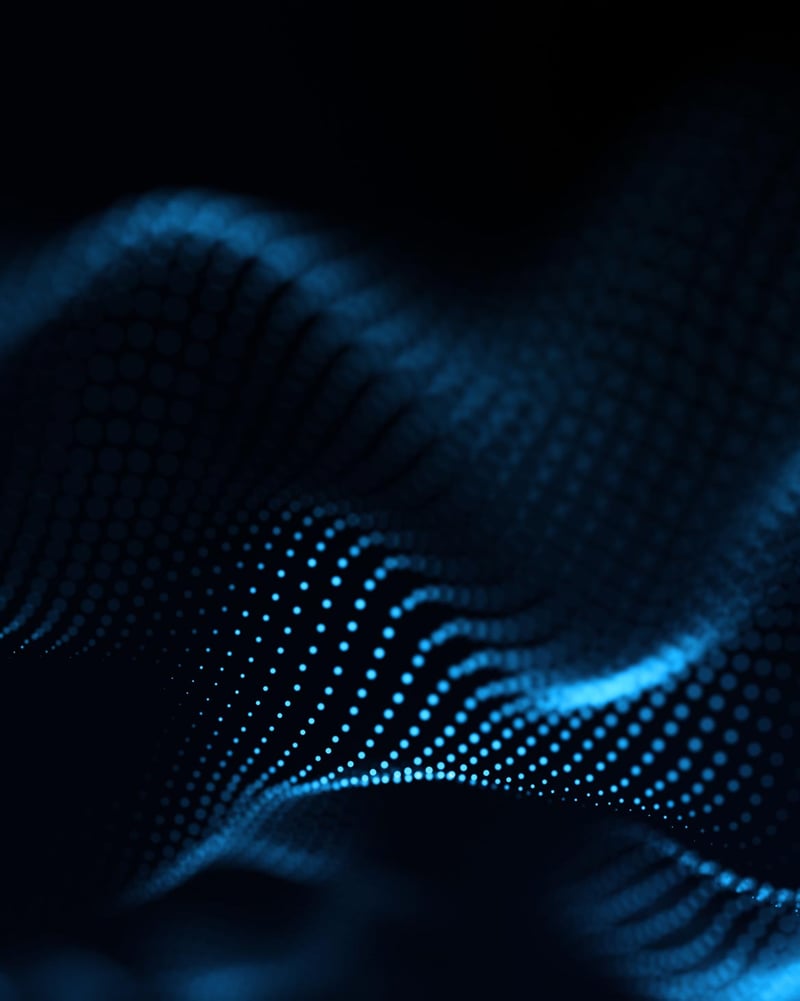
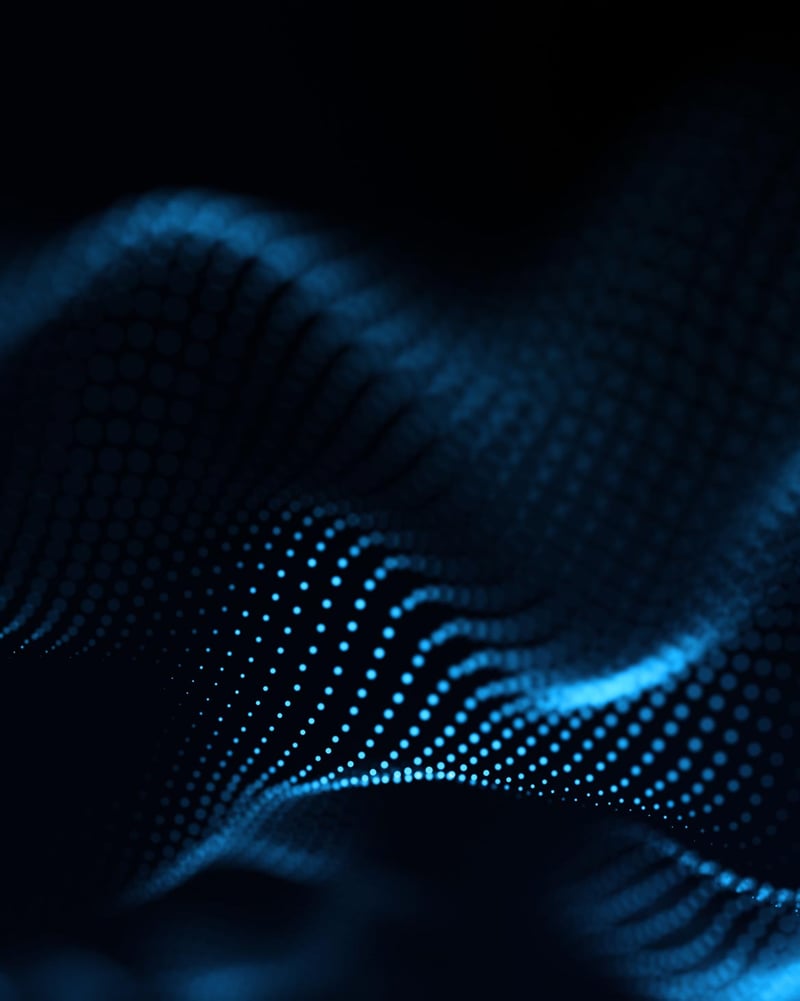
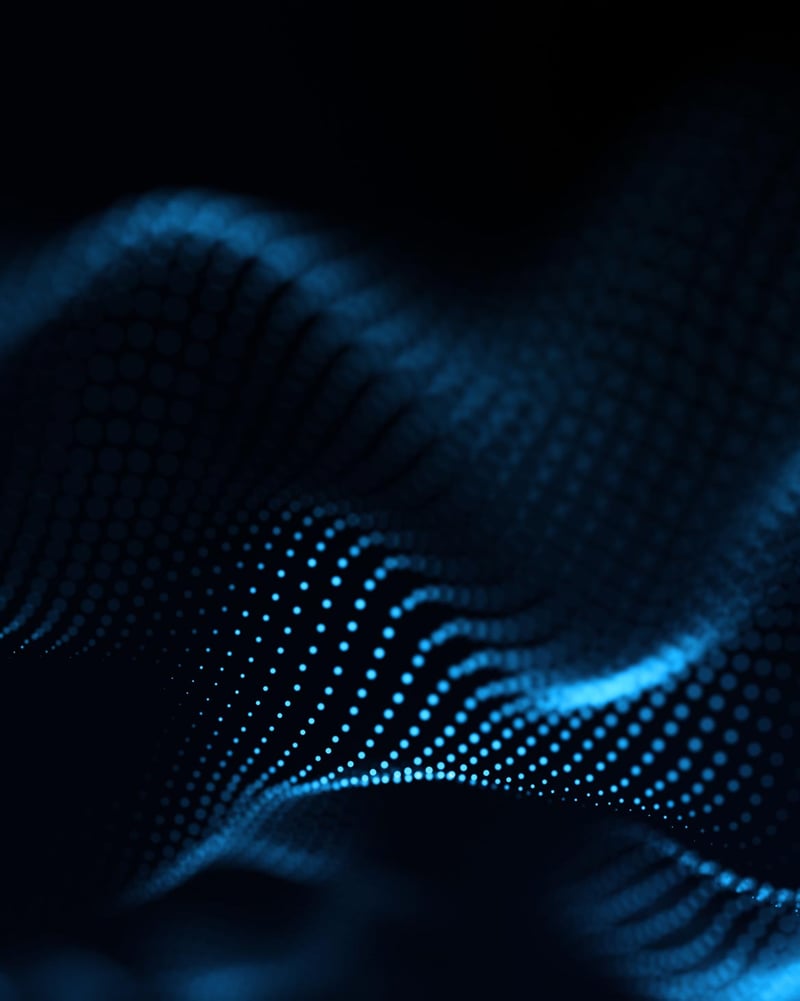
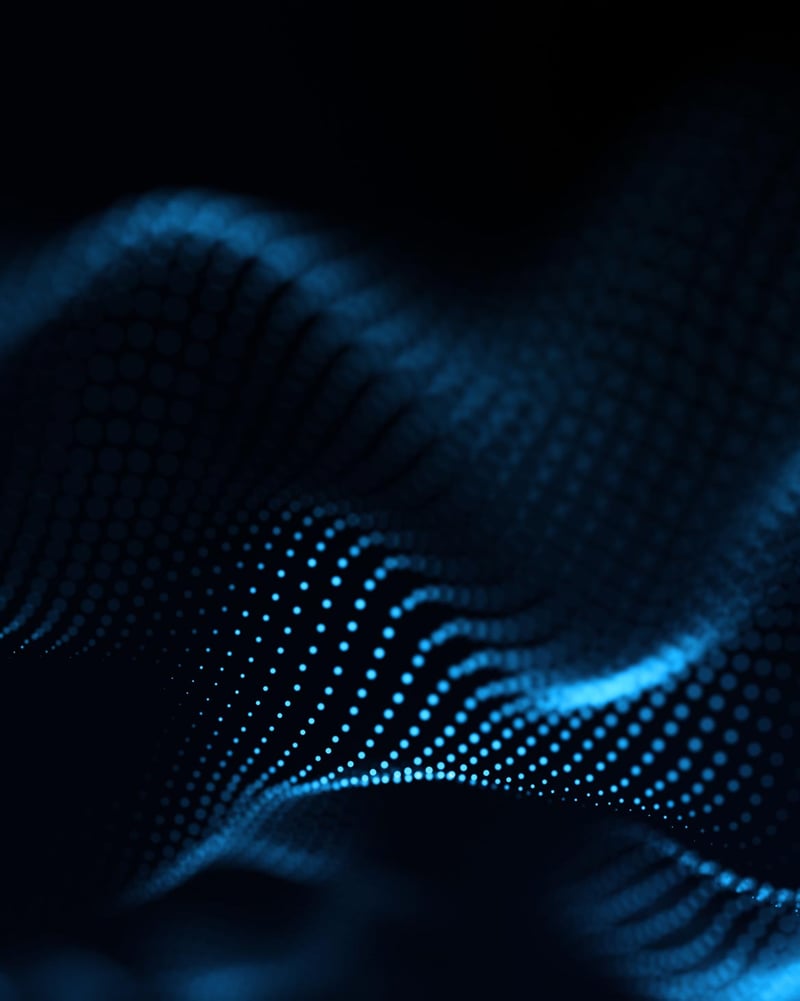
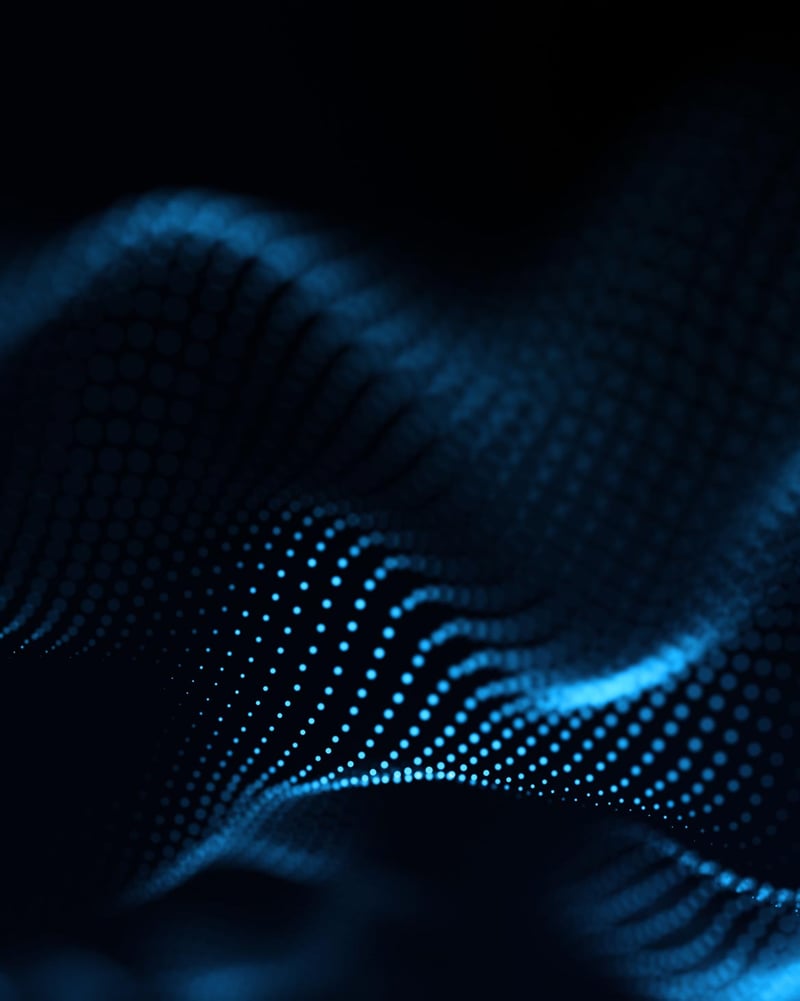
They already use CANEA ONE
Implementation
and validation
All new versions of CANEA ONE that are developed are verified against the overall requirements of FDA Part 11, MDR, GMP etc. In order to validate a system like CANEA ONE, we need input from the standard product and from the client project. Because the standard CANEA ONE product is verified and is provided with some documentation already completed, the entire validation process is facilitated for you.
We offer the following document templates and use them together with our clients to cover the requirements for a validated system in the Life Science industries:
User Requirements Specification (URS).
The document must contain the requirements placed on CANEA
ONE from a functional, process, and user perspective. Regulatory requirements must also be taken into account. Usually designed by the client, CANEA can provide documentation linked to product-specific requirements to facilitate system requirements definition.
Risk analysis.
Document designed by the client in connection with the risk analysis carried out. The risk analysis must identify and highlight the risks associated with the use of CANEA ONE. The risk mitigation plan must be implemented by identifying appropriate activities, such as verification through testing, training activities
etc.
Function specification.
This document must contain answers on how we meet the requirements placed on CANEA ONE in the requirements specification. Designed by CANEA in response to the client.
Document designed by CANEA that provides the configuration that has been applied in the client's specific CANEA ONE system.
Design Review.
The meeting between us and the client where we make a reconciliation between URS and Function Specification/Design Specification
Validation plan.
Document that defines how the validation of CANEA ONE will be carried out. The document must include a validation strategy that clarifies roles, responsibilities, validation activities and boundaries of the validation effort.
Qualification.
Test plans and test cases (IQ,OQ,PQ) must be designed to verify that CANEA ONE works as expected and meets the requirements that have been placed on the system, as well as the risks that have been identified related to its field of use.
Validation report.
Document that establishes the outcome of the validation effort. The report must contain information certifying that the CANEA ONE system has been validated and meets the requirements that have been placed on it.
CANEA’s expertise and ability to provide guidance during the preparation of the structure of the system is something we have not experienced with previous suppliers. I highly recommend CANEA ONE to other organizations within Life Science in need of e-signatures, read receipts and traceability. The system is flexible when necessary and robust when required.
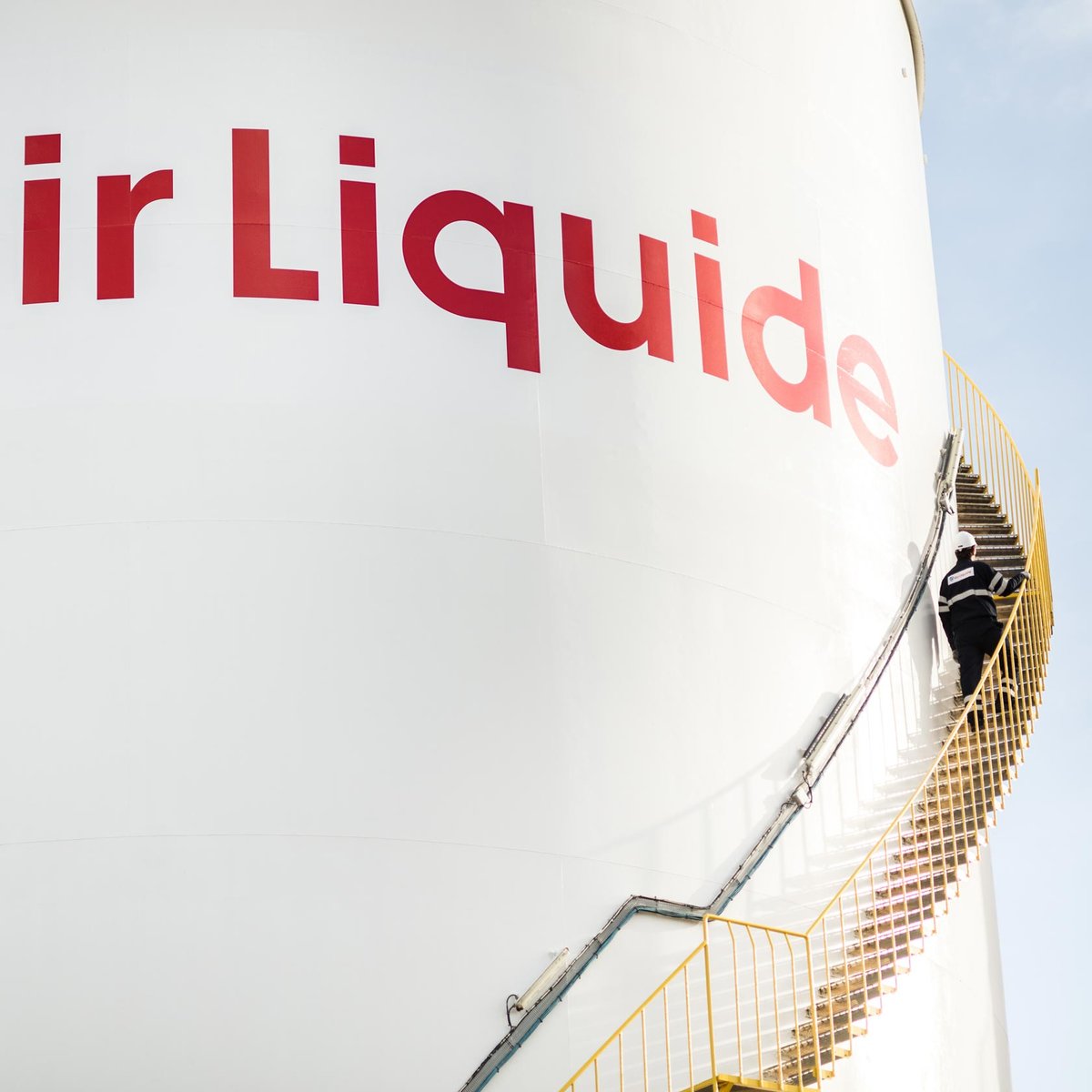
Some of our clients
CANEA has helped hundreds of organizations become both more efficient and more profitable. Here are some examples of what we've worked on so far.

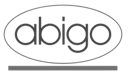
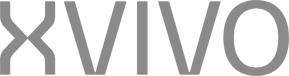
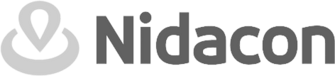
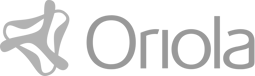
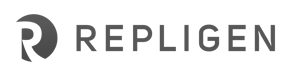
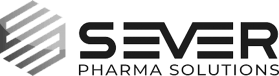

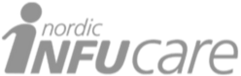
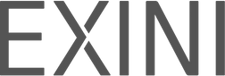
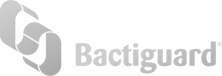
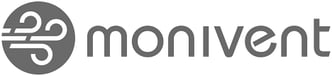
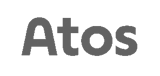
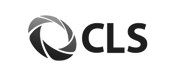

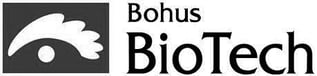
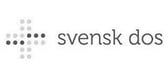
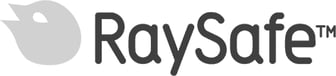
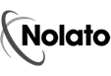
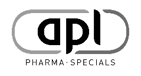
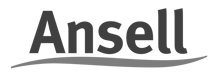

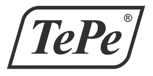
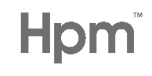

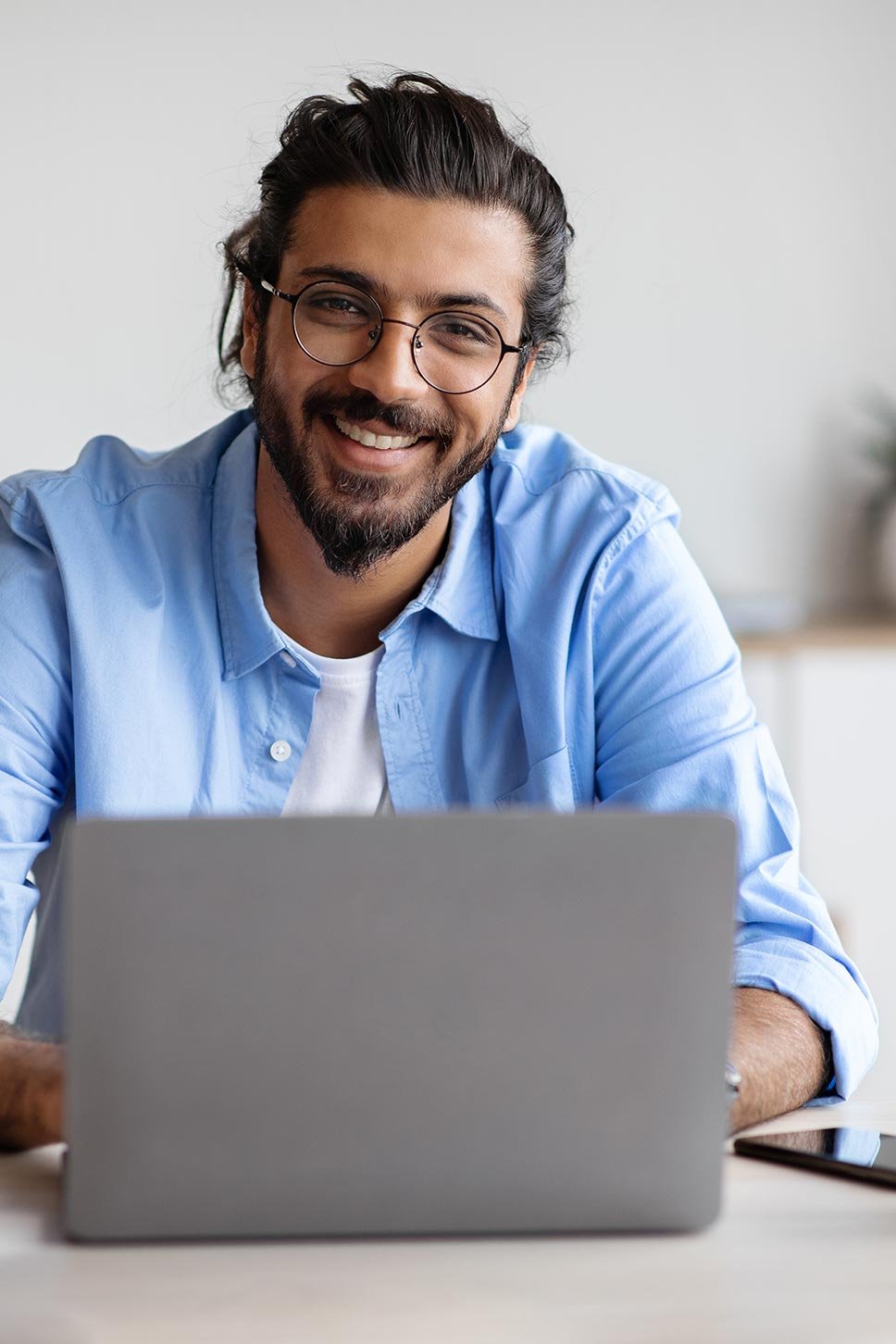
Book a demo
Fill in the form to book a personal demo.