Falkenberg on the Swedish west coast is home to one of Europe's most modern rollforming facilities – Bendiro Profile Tech. It manufactures customized rollformed profiles for industrial companies in a wide range of sectors.
After a period of rapid growth, the company is now in the process of moving to larger and more modern premises with both new and upgraded machinery and production lines. To increase productivity, shorten set-up times and reduce the number of errors in production, in the form of too much scrap and incorrect stock balances, the Six Sigma Green Belt training project was initiated under the auspices of CANEA.
Long set-up times
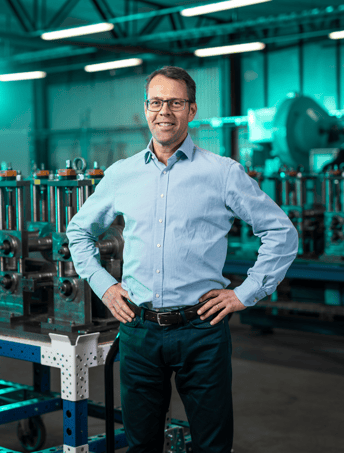
Sheet metal roll-forming is a manufacturing technique with a wide range of benefits, but one of its challenges is long set-up times. The machines used are complex and changeovers from one product to another take time, sometimes several days. To meet customers' needs more quickly and efficiently, it is important to reduce both set-up times and the amount of scrap.
– We initiated the Green Belt project to learn a new way of problem-solving and to be able to tackle our challenges in a more systematic and fact-based way. A lot of it is about the productivity of the machines, things like reducing our downtime and scrap rates. These are areas where we know there is room for improvement, says Rasmus Särnblad, CEO of Bendiro.
The Green Belt training
Bendiro selected a handful of key people for a Six Sigma Green Belt training camp and each participant was given their own project to train on. The training, which started in 2023, consisted of three stages of two full days each. The first two stages ended with a homework assignment and participants were given the opportunity to check in with CANEA's consultant in the meantime. The sixth and final day ended with a presentation and examination.
– I was tasked with looking at set-up times, where we have now started to get a little better control. Previously, when we shut down a machine, what we call “set”, there was not enough focus on how long it took in relation to the budgeted time or how long it should really take, says Niklas Alfredsson, team leader for the set operators, and continues:
– We pre-set some parts of the rolls outside the machine, but sometimes there was a sudden set-up without us having time to pre-set. This in turn meant that we had to set in the machine, resulting in a longer production break than necessary. When we started focusing on the setting process itself, instead of the cost of the setting operators, we cut a lot of time. In one of the roll-forming machines, we have reduced the set-up time from 24.5 hours to 5.5 hours, and in a welding line, we have reduced the set-up time from 330 minutes to 45 minutes!
Big savings to be made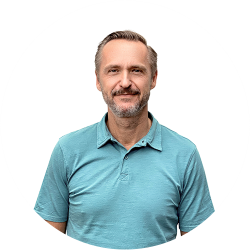
So far, it has been a relatively small group of Bendiro employees who have worked methodically to streamline production, but that will change because there are so many savings to be made in this area.
– We are still a bit unaccustomed to working in such a structured way with the different steps, so there is still a lot to gain, but the more times we do this, the faster and more efficient it will be. Whatever we look at, we will be able to recoup the costs of the improvement work, says Quality & Environment Manager Daniel Hellberg, who has been investigating how to reduce the amount of scrap, and adds:
– We hope that in the long run, we will also be able to reduce the capital tied up in the raw materials warehouse, especially as we have coped relatively well with the supply chain crises that have characterized the world during the coronavirus pandemic and its aftermath. On the other hand, we also offer storage of ready-made profiles for faster call-offs and delivery, but we can share the costs with customers. For example, we have a customer in France where we have a warehouse that they can call on.
CANEA's value-added contribution
– CANEA has helped us to create a structure for how to measure. As a result, we have discovered many shortcomings that we have been able to address to produce better results. Now we measure and analyze the data in the right way, which means that we create the right conditions for the improvement measures, says Niklas Alfredsson, and continues:
– We have scratched the surface and are heading in the right direction. We have done some things, but we have much more to implement. For example, the instructions to the operators must be much better to shorten stops.
– One good thing about the training program has been what has emerged in the meetings we have had. Normally, you are often running around the business and are stressed, but the meetings have meant that we have been able to meet in peace and discuss both problems in the business and what tools we should use in the improvement work. It has been very positive, so we must not lose this important forum in the future, says Daniel Hellberg, adding:
– We are in an interesting phase where we are currently picking the lowest-hanging fruits and thus getting a big return on the improvements made. But as we get better, it will of course become harder and harder to improve. That's why it's important to have the methodology in place so that we constantly make correct analyses that lead to the desired improvements.
CEO Rasmus Särnblad concludes:
– I think it has worked well with the combination of teacher-led training sessions and own project reviews, where CANEA's consultant has supported the students. As a trainer, it is important to find the right level of guidance and support, and I think CANEA has done that.
“CANEA has the ability to convey a systematic approach and methodology and combine it with the experience of having worked with other companies in different industries.”
Rasmus Särnblad, CEO Bendiro Profile Tech
Interested in knowing more?
We create the right conditions for a vibrant management system with better opportunities to realize the strategy and increase profitability.